Plastics extrusion is a popular manufacturing process that allows the production of various parts with fixed cross-sectional profiles. This process involves the use of an extruder, which contains a rotating screw enclosed in a heated barrel. The material is mixed and melted inside the extruder, then passed through a die, which shapes the molten plastic material into the desired form.
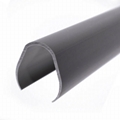
This article will discuss the various types of plastic extrusion processes including film extrusion, sheet extrusion, pipe, profile and tubing extrusion.
Film Extrusion
Film extrusion is the process of creating thin, flexible sheets of plastic film, typically used in packaging applications. It involves using a flat die that spreads the molten plastic into a thin, flat sheet. This sheet is then cooled, rolled up, and cut into smaller rolls.
Film extrusion can be further classified into blown film extrusion and cast film extrusion. Blown film extrusion involves blowing the molten plastic into a bubble using air pressure. The bubble is then reduced to a flat sheet, which is wound into rolls. Cast film extrusion, on the other hand, uses a chill roll to cool and solidify the molten plastic into a sheet.
Sheet Extrusion
Sheet extrusion is the process of producing flat sheets of plastic material used in various applications including automotive, signage, and construction. Sheet extrusion involves the use of a flat die to shape the molten plastic material into a thin sheet. The sheet is then cooled, trimmed, and cut to the desired size.
Pipe Extrusion
Pipe extrusion is the process of creating plastic pipes and tubes for use in plumbing, electrical conduit, and other applications. The process involves using a screw extruder, which melts and mixes the plastic material before forcing it through a shaping die. The die gives the pipe its shape and size before it is cooled and cut to the desired length.
Profile Extrusion
Profile extrusion is the process of creating plastic profiles or shapes with a fixed, cross-sectional profile. This process is commonly used in window and door frames, decking, and other construction applications. Profile extrusion involves placing the molten plastic material into a die with the desired shape and forcing it through using a screw or ram.
Tubing Extrusion
Tubing extrusion is the process of creating plastic tubes with a fixed, cross-sectional profile for use in medical, automotive, and other applications. This process involves using a screw extruder to melt the plastic material before forcing it through a shaping die. The die shapes the tube into the desired size and shape before it is cooled and cut to the desired length.
Conclusion
In conclusion, plastics extrusion is a versatile manufacturing process that allows the production of various parts with fixed cross-sectional profiles. The process involves the use of an extruder, which melts and shapes the plastic material into the desired form using a die. The types of plastic extrusion processes discussed in this article include film extrusion, sheet extrusion, pipe extrusion, profile extrusion, and tubing extrusion. Each process has its unique set of advantages and is suitable for specific applications.