High Density Polyethylene (HDPE) remains one of the most commonly used thermoplastics in the manufacturing industry. It is known for its durability, resistance to weathering, and versatility in applications. With the increasing demand for HDPE products, manufacturers are looking for ways to optimize the production process and ensure consistent quality output. This is where extrusion comes into play.
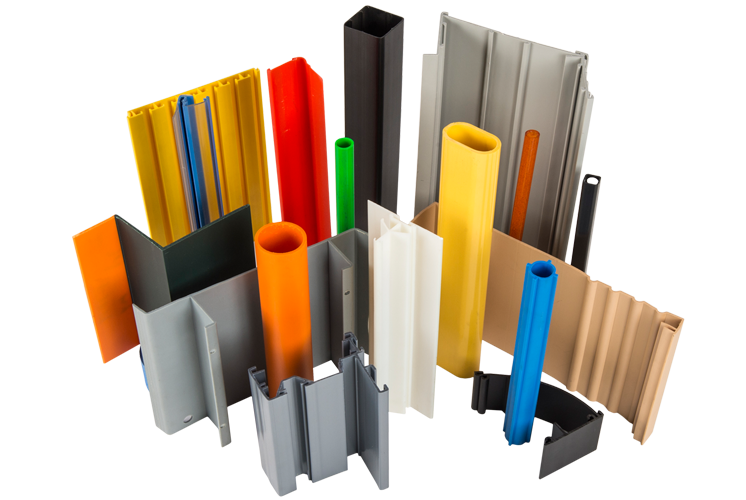
Teel Plastics is a leading manufacturer of custom extruded plastic components, with specialization in HDPE profile extrusion. Their extruder has the capability to handle a wide range of resins, including PP, TPU, flex PVC, FEP, and PEEK (brand name removed). This article highlights the benefits of extrusion and the various factors that contribute to the success of HDPE profile extrusion.
What is Extrusion?
Extrusion is a manufacturing process that involves forcing a heated thermoplastic material through a die to create a continuous cross-section profile. This profile can be cut to the required length and shape to produce a final product. Extrusion is a highly versatile process that can be used to create a wide variety of plastic parts, including pipes, tubes, and profiles.
The extrusion process begins with the selection of the appropriate resin material. HDPE is a common choice for high strength and rigidity applications. The selected resin is then fed into the extruder hopper, where it is melted and forced through a die that shapes the molten plastic into the desired profile.
Benefits of Extrusion for HDPE Profile
Extrusion is a highly versatile process that offers many benefits for HDPE profile extrusion. These include:
1. Faster production: Extrusion is a continuous process that can produce high-quality HDPE profiles at a faster rate. This makes it an ideal process for mass production.
2. Consistent quality: Extrusion ensures consistent quality of HDPE profiles, a key factor in meeting customer demands and ensuring product quality.
3. Cost-effective: Extrusion offers cost-effective production of HDPE profiles, making it the ideal process for high volume and long production runs.
Factors Contributing to Successful HDPE Extrusion
The success of HDPE profile extrusion depends on several factors such as:
1. Die Design: The design of the die is critical to the success of HDPE profile extrusion. Proper die design ensures uniform flow of the molten plastic, resulting in uniform profile and wall thickness.
2. Extruder temperature: The extruder temperature must be carefully monitored and controlled to ensure the proper melt viscosity of the HDPE material.
3. Line speed: The line speed at which the HDPE profile is extruded must be carefully controlled to ensure proper cooling of the material and to avoid deformation.
4. Material Properties: The properties of the HDPE material, such as melt viscosity, density and molecular weight distribution, must be managed to ensure optimal performance.
Conclusion
Teel Plastics offers HDPE profile extrusion services that meet the highest industry standards. They use advanced extrusion equipment and cutting-edge technology to ensure consistent quality and high output. With their expertise in HDPE profile extrusion, they can help manufacturers optimize their production process and reduce costs while meeting their customers' demands for high-quality products.
In conclusion, extrusion is the key to producing high-quality HDPE profiles. It offers faster production, consistent quality, and cost-effectiveness. With the right equipment and expertise, manufacturers can optimize their extrusion process and offer their customers innovative and reliable products.