Manufacturing processes play a crucial role in bringing products to the market, and among those processes is the extrusion molding process. With its high production capacity, consistency, and precision, it is used in a wide range of industries, from packaging and construction to aerospace and automotive.
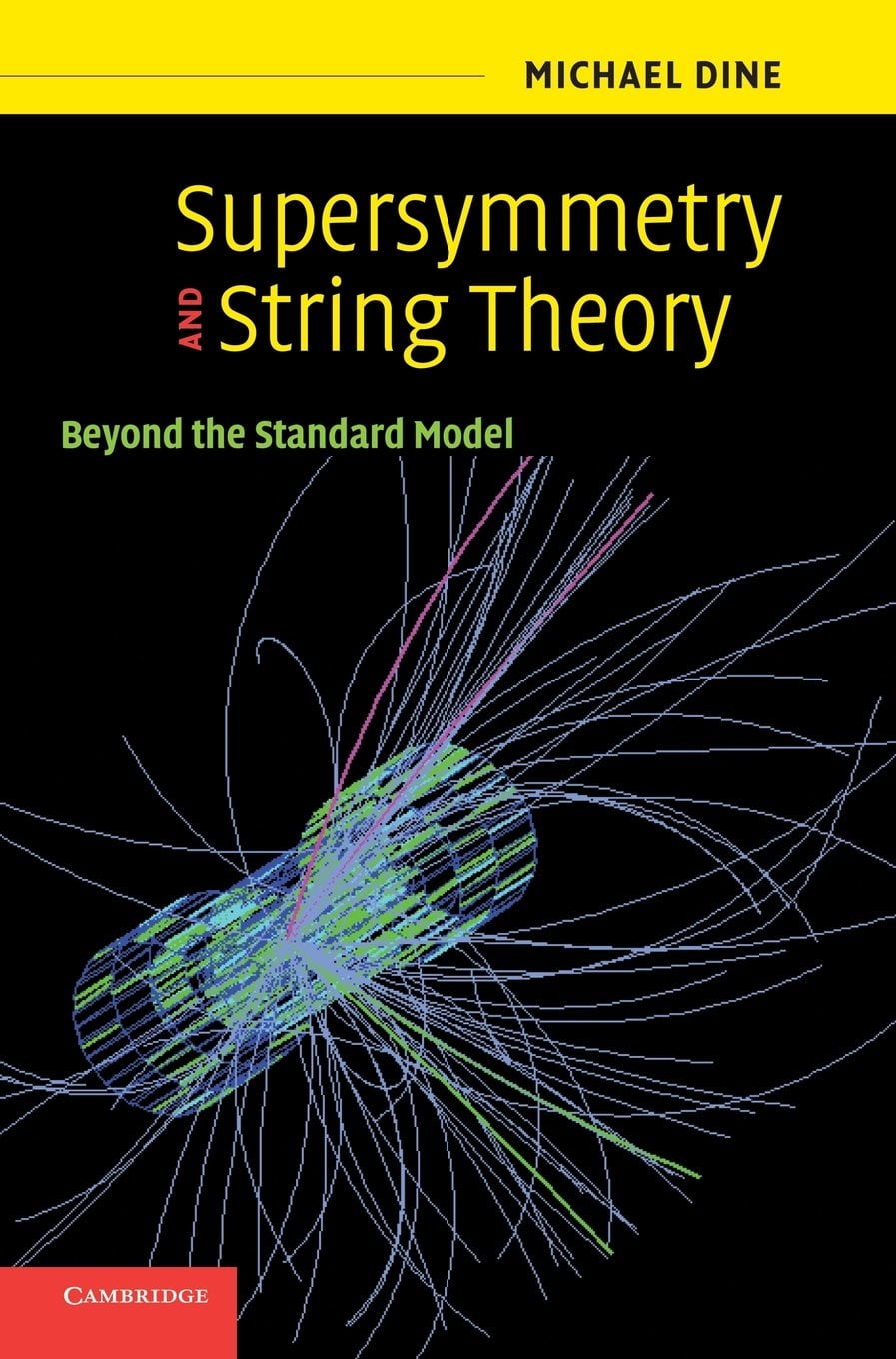
In this blog, we will cover all aspects of the extrusion molding process, from the definition and types to the advantages and challenges. We will also highlight some of the applications of extrusion molding and provide tips for optimizing the process to achieve effective results.
What is Extrusion Molding Process?
Extrusion is a manufacturing process that involves pushing a molten material through a die to create a continuous profile. The material can be a thermoplastic, thermoset, metal, or composite. The process requires a high-temperature extruder, which melts and transports the material to the die, where it is shaped into the desired cross-sectional shape.
Extrusion has two primary types: hot and cold. Hot extrusion involves heating the material to its melting point and then forcing it through the die. Cold extrusion, also known as cold forming, involves shaping the material below its recrystallization temperature, typically through a combination of pressure and shear.
Advantages and Challenges of Extrusion Molding Process
The extrusion molding process offers several advantages over other manufacturing methods, including:
1. High production capacity: Extrusion allows for the continuous production of profiles, which can be cut into specific lengths afterward. This results in higher production rates and lower labor costs.
2. Consistent quality: Extrusion offers precise control over the shape and dimensions of the profile, resulting in consistent quality products.
3. Versatility: Extrusion can be used with a wide range of materials, including plastics, metals, and composites. It can also produce profiles of various shapes and sizes, from tubes and rods to sheets and films.
However, extrusion also comes with some challenges, such as:
1. Material selection: The material used in extrusion must have suitable rheological properties, such as fluidity and viscosity, to ensure proper flow through the die.
2. Die design: The die design is essential in determining the final shape and dimensions of the profile. A poorly designed die may result in defects or inconsistencies.
Applications of Extrusion Molding Process
The extrusion molding process is used in several industries, including:
1. Packaging: Extruded films and sheets are commonly used in food packaging, such as cling wrap and vacuum packaging.
2. Construction: Extruded profiles are used in the construction industry for window and door frames, roofing, and wall cladding.
3. Automotive: Extruded profiles are used in the automotive industry for bumpers, trim, and weather sealing.
4. Aerospace: Extruded profiles are used in the aerospace industry for structural components.
Tips for Optimizing the Extrusion Molding Process
Optimizing the extrusion molding process can lead to improved quality and increased production efficiency. Here are some tips for optimizing the process:
1. Use quality materials: Thoroughly test the material to ensure that it has the necessary rheological properties for the process.
2. Optimize die design: The die design is critical and should be optimized for the material and profile being produced.
3. Monitor temperature: Temperature is a critical parameter in extrusion and should be closely monitored and controlled.
4. Monitor extruder output: Monitoring extruder output can help identify potential problems early on and minimize waste.
5. Use post-extrusion equipment: Post-extrusion equipment, such as cooling and cutting systems, should be optimized for the product being produced.
Conclusion
The extrusion molding process is a versatile and widely used manufacturing technique that allows for the mass production of profiles with consistent quality. The process has several advantages but also comes with some challenges. By following the tips and best practices outlined in this blog, companies can optimize the process and achieve effective results.