Cast film extrusion is a popular manufacturing process used to produce a wide range of products, including plastic films, food packaging, medical packaging, and industrial wraps. The process involves melting and extruding a polymer material through a flat die, which is then stretched and cooled on a cooling roll. The final product is a thin, flexible film with a variety of properties and applications.
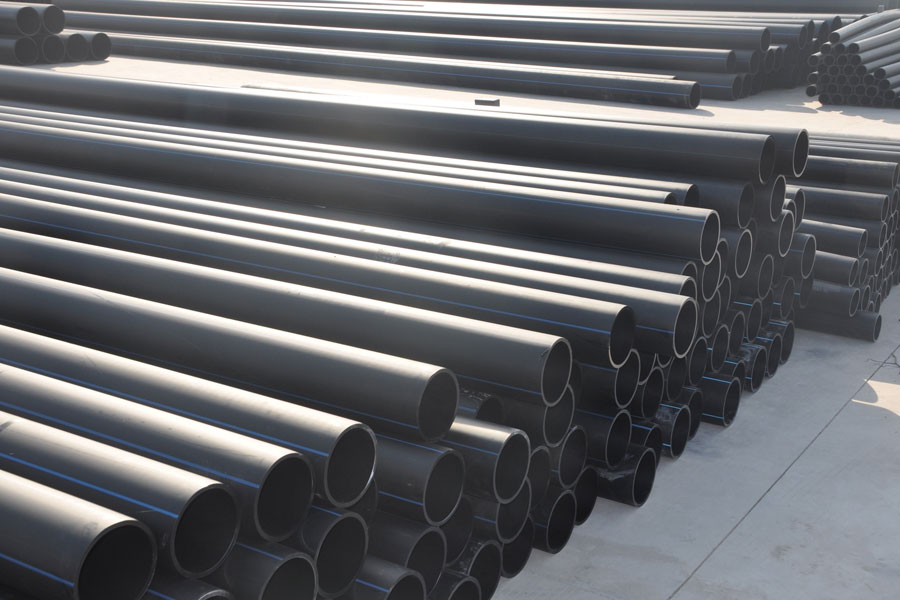
The Basics of Cast Film Extrusion
In the cast film extrusion process, the polymer material is first melted in a heated extrusion barrel. The molten resin is then forced through a flat die, which shapes the film to the desired thickness and width. The extruded film is then drawn by a pair of nip rollers and onto a cooling roll. As the film is drawn, it is cooled by the cooling roll, which solidifies the material and provides good surface quality for the film.
The thickness of the extruded film is determined by the distance between the die and the cooling roll, which is known as the draw gap. The draw ratio, or the ratio of the thickness of the extruded film to the thickness of the polymer material, is typically around 20:1. This high draw ratio allows the polymer material to be stretched and thinned, resulting in a thin and uniform film.
The Advantages of Cast Film Extrusion
The cast film extrusion process offers a number of advantages over other manufacturing processes, such as blown film extrusion and extrusion coating. One of the main advantages is the ability to produce films with superior clarity and uniformity. The process provides excellent control over the thickness and width of the film, allowing for consistent product quality and performance.
Another advantage of cast film extrusion is the high line speeds it can achieve. The process can produce films at speeds of up to 500 meters per minute, making it highly efficient and cost-effective. Additionally, the process is highly scalable and can be easily adapted to meet changing market demands.
The Applications of Cast Film Extrusion
Cast film extrusion is used in a wide range of applications, due to the versatility of the final product. Some of the most common applications include:
- Packaging: Cast film extrusion is used to produce a wide range of packaging materials, including food packaging, medical packaging, and industrial wraps. The films can be designed to provide specific properties, such as barrier resistance or oxygen permeability, to meet the requirements of the application.
- Labels: Cast film extrusion is used to produce pressure-sensitive labels for a range of applications. The films can be printed with high-quality graphics and designs, and can be applied to a range of surfaces.
- Laminates: Cast film extrusion can be used to produce multi-layer films, which are used in a range of applications. The films can be designed to provide specific properties, such as barrier resistance or UV stability, to meet the requirements of the application.
Conclusion
Cast film extrusion is a highly versatile and efficient manufacturing process, which is used in a wide range of applications. The process offers excellent control over the thickness and width of the film, allowing for consistent product quality and performance. Additionally, the process is highly scalable and can be easily adapted to meet changing market demands. With its many advantages, cast film extrusion is a popular choice among manufacturers looking to produce high-quality films and packaging materials.