Plastic extrusion is a popular manufacturing process used to create a variety of plastic products such as pipes, tubes, films, and sheets. The process involves melting plastic raw materials and then forcing them through an extruder, a machine with a screw that rotates and pushes the molten plastic through a die. The screw is one of the most critical components of an extruder, and its design plays a crucial role in the quality of the end product. In this article, we will look at the importance of plastic extruder screw design and its impact on the extrusion process and output.
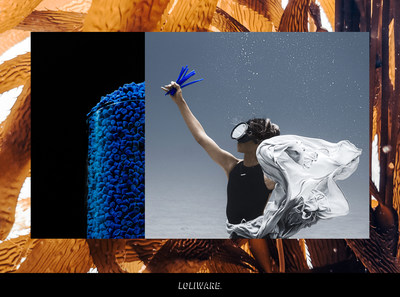
Understanding Plastic Extruder Screw Design
The design of an extruder screw is a complex process that requires an understanding of the polymer chemistry and rheology, material properties, and the process conditions. The screw design must be optimized to achieve the desired output in terms of product quality, throughput, and energy efficiency. Typically, the screw design is customized for a particular polymer type, viscosity, and processing temperature.
The screw consists of three critical parts: the feed section, the compression section, and the metering section. The feed section is responsible for feeding the raw materials into the extruder, while the compression section compresses and melts the polymer. The metering section controls the flow rate and pressure of the molten polymer as it exits the die. Each section has a particular design configuration and pitch, depending on the material and process requirements.
Factors Affecting Screw Design
Several factors affect the design of an extruder screw, including the polymer type and grade, fillers, additives, and processing conditions. The screw must be designed to accommodate the specific properties of the material to ensure high-quality output. For instance, polymers with high viscosity and shear sensitivity require a screw with a deeper feed section to facilitate uniform melting and mixing. Similarly, fillers such as talc and calcium carbonate require a screw with more compression to avoid separation and poor dispersion.
Benefits of Optimized Screw Design
Optimizing the screw design has numerous benefits for plastic extrusion manufacturers. These include;
1. Improved product quality – Optimized screw design ensures consistent mixing and melting of the polymer, resulting in high-quality output with minimal defects.
2. Increased throughput – An optimized screw design increases the extrusion rate, thereby improving the throughput and reducing production time.
3. Energy efficiency – A properly designed screw reduces energy consumption by minimizing the pressure drop and increasing the melting rate.
4. Reduced wear and tear – A properly designed screw reduces wear and tear on the extruder components, reducing the maintenance costs and downtime.
Conclusion
In conclusion, the screw is a critical component of plastic extrusion, and its design is fundamental to the quality of the end product. The screw design must be customized to accommodate the specific material properties and processing conditions to achieve optimal output. Manufacturers must work with experienced screw designers to develop a reliable screw design that delivers consistent and high-quality output. If you need to design screws for your extruder, you can find experienced designers with a reputation for delivering quality designs. Contact us today to learn how we can help you with your screw design needs.