Polypropylene extrusion process is the process of pushing molten polypropylene through a die to create a continuous shape. This process is widely used to create plastic products, including pipes, packaging, and even toys. The process is relatively simple, but it requires a thorough understanding of the material properties and processing conditions.
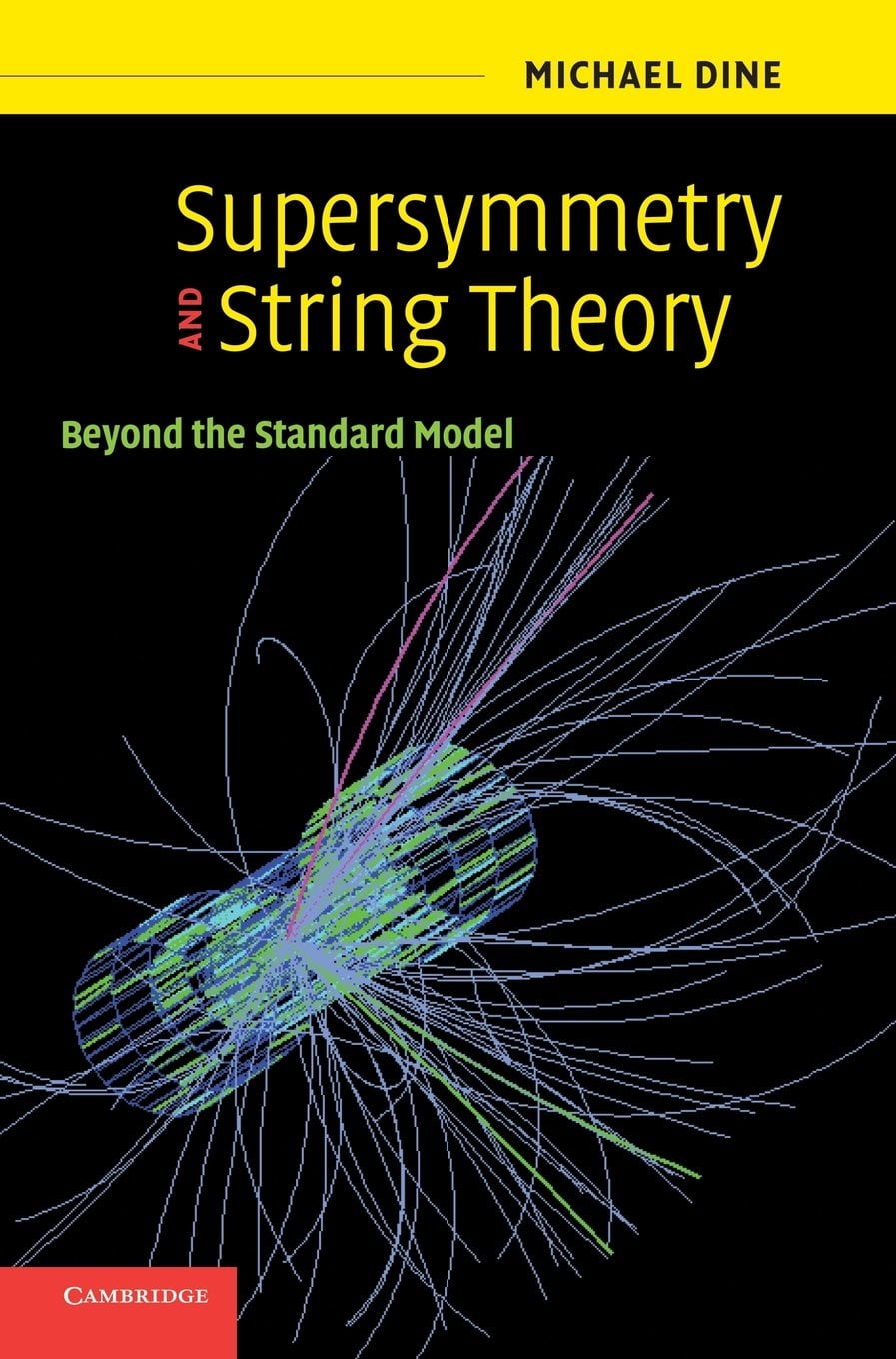
What is Polypropylene?
Polypropylene (PP) is a thermoplastic polymer used in a wide range of applications. It is a versatile material with a combination of mechanical, thermal, and chemical properties. PP is used in packaging, textiles, automotive parts, and construction materials, among others. It is a preferred material for extrusion due to its good flow properties, low density, and good impact resistance.
The Extrusion Process
Extrusion is a manufacturing process that involves pushing a material through a die to create a continuous shape. The process works by melting the material and then forcing it through a die that has the desired shape. The extruded material is then cooled and cut to the desired length. The process is used to create a wide range of products, including pipes, tubes, profiles, sheets, and films.
The polypropylene extrusion process involves several steps:
1) Material Preparation: The polypropylene pellets are typically dried before use to remove any moisture, which can affect the properties of the material. The pellets are then fed into the extruder, which melts the material.
2) Extrusion: The melted polypropylene is forced through a die that has the desired shape, typically a circular profile for pipes or a rectangular profile for sheets. The extruded material is then cooled using water or air and may be drawn down to reduce its diameter or thickness.
3) Cutting and Finishing: Once the extruded material is cooled, it is cut to the desired length and may be further processed, such as embossing or printing.
Factors Affecting the Process
Several factors affect the polypropylene extrusion process, including:
1) Temperature: The temperature of the extruder and die must be carefully controlled to ensure the material flows properly and has the desired properties.
2) Pressure: The pressure inside the extruder must also be carefully controlled to avoid any voids or defects in the final product.
3) Die Design: The die design is critical in creating a uniform cross-section and preventing defects. The die must be designed to accommodate the flow properties of the material and the desired shape of the product.
Applications
Polypropylene extrusion is used in a wide range of applications, including:
1) Pipes and Fittings: Polypropylene pipes and fittings are used in a variety of industries, including plumbing, irrigation, and chemical processing.
2) Packaging: Polypropylene is used for packaging products such as food and drink containers, bags, and shrink wrap.
3) Construction Materials: Polypropylene sheets and profiles are used in construction for roofing, cladding, and insulation.
Conclusion
Polypropylene extrusion process is a critical process in a wide range of industries. The process works by melting the material and then pushing it through a die to create a continuous shape. The process requires careful control of temperature, pressure, and die design. The result is a wide range of products, including pipes, packaging, and construction materials that are essential to our daily lives. If you need a high-quality extrusion product, look no further than polypropylene extrusion.