Introduction:
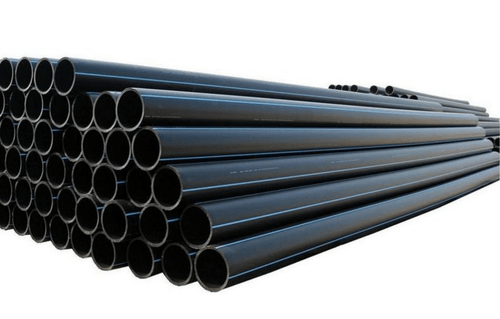
High-density polyethylene (HDPE) double-wall corrugated pipes have emerged as widely used sewage and drainage solutions in our daily lives. Manufactured using HDPE as the primary raw material, these pipes have revolutionized the industry with their exceptional durability, strength, and cost-effectiveness. In this blog post, we will delve into the intricate details of the processing methods employed in the production of HDPE drainage sheets.
1. Understanding High-Density Polyethylene (HDPE):
Before diving into the manufacturing process, it is crucial to comprehend the key characteristics of HDPE. High-density polyethylene is a thermoplastic known for its excellent tensile strength, chemical resistance, and weatherability. Its versatility, UV resistance, and recyclability make it a sought-after material for various applications, including sewage and drainage systems.
2. Raw Material Preparation:
The initial stage of HDPE drainage sheet production involves the careful selection and preparation of high-quality raw materials. HDPE resin pellets are typically used, as they maintain the polymer's properties during the manufacturing process. The pellets are inspected, sorted, and processed to eliminate any impurities, ensuring a superior-quality end product.
3. Extrusion Process:
Extrusion is a crucial step in the manufacturing process of HDPE drainage sheets. The selected HDPE resin pellets are fed into an extruder, which consists of a screw mechanism. The extruder then heats and melts the pellets, forming a semi-solid HDPE material. The molten HDPE is then forced through a die, where it takes the shape of the desired corrugated sheet. The extrusion process allows for the customization of sheet thickness, width, and corrugation patterns.
4. Corrugation and Cooling:
Once the shaped HDPE sheet exits the die, it is passed through a corrugating unit. Here, the sheet is pressed through specially designed rollers to create the characteristic corrugated pattern. This corrugation imparts structural strength, helping HDPE drainage sheets withstand heavy loads and external pressures. Subsequently, the corrugated sheets are cooled using water or air cooling methods, ensuring their dimensional stability.
5. Quality Control and Testing:
To ensure the reliability and longevity of HDPE drainage sheets, rigorous quality control measures are implemented throughout the production process. Samples from each batch are subjected to various tests, including tensile strength, impact resistance, and dimensional checks. Maintaining strict quality standards guarantees that only high-quality HDPE drainage sheets reach the market.
6. Final Product:
Once the production process is complete and the HDPE drainage sheets pass all quality tests, they are cut into desirable lengths and packaged for distribution. These sheets are often supplied with additional features such as UV stabilization and perforations to enhance their suitability for specific applications.
Conclusion:
The processing methods of HDPE drainage sheets play a pivotal role in ensuring the final product's quality, durability, and performance. High-density polyethylene's versatility and inherent properties make it an excellent choice for sewage and drainage systems. By understanding the intricacies involved in the production of HDPE drainage sheets, we can appreciate the significance of this material in our everyday lives while recognizing the role it plays in building sustainable and reliable infrastructure.
Keywords: High-density polyethylene, HDPE, drainage sheets, production, processing methods, extrusion, corrugation, quality control, durability, sewage and drainage systems.