Compound extruders are an essential tool for many industries as they enable the production of a wide range of materials such as plastics, rubber, and other compounds. However, like any manufacturing process, there is always room for improvement which can lead to better product quality, increased efficiency, and cost savings. Process optimization is an ongoing effort to improve the efficiency and effectiveness of a production process, and with the help of modern technology, there are many ways to achieve this goal.
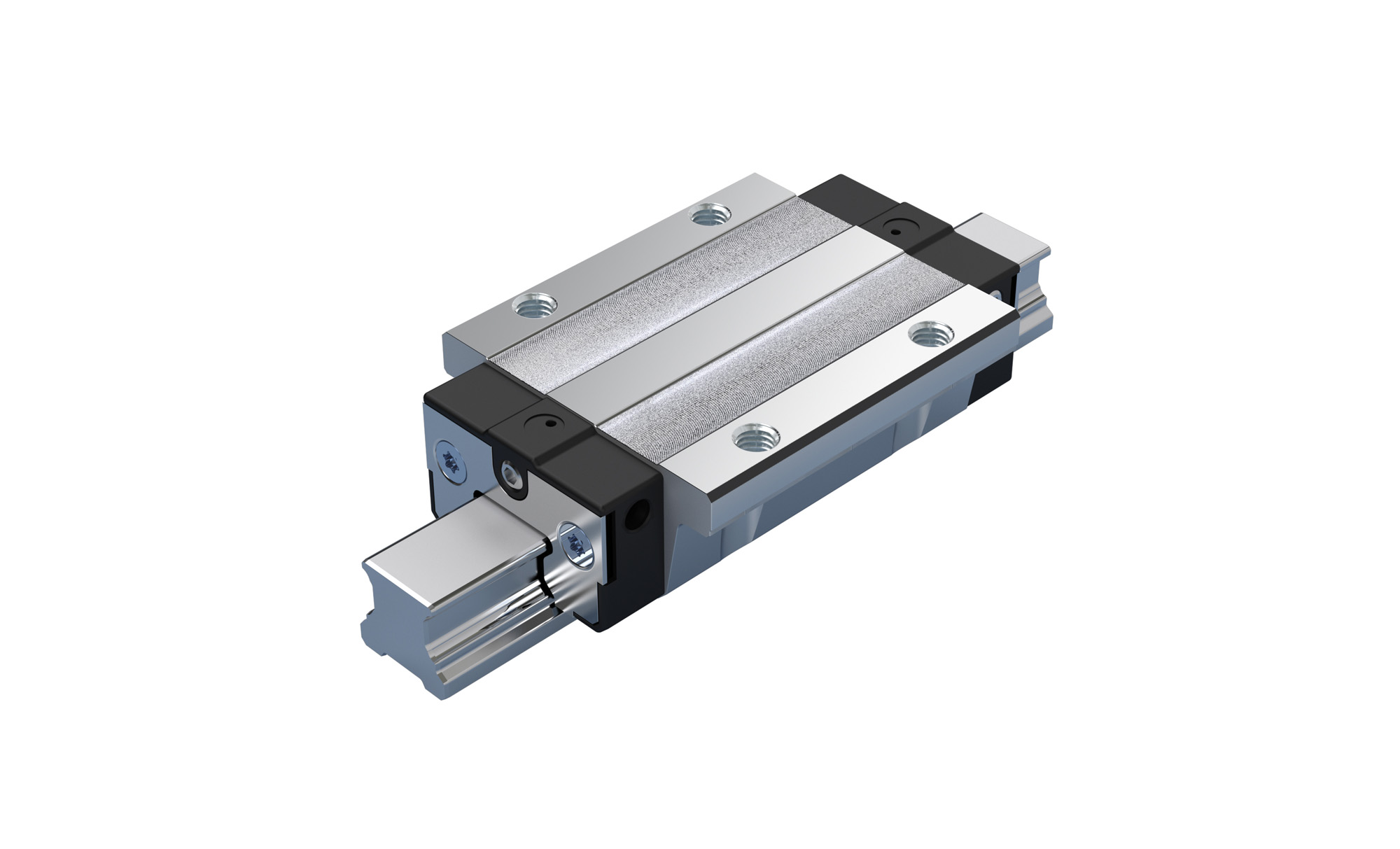
One of the most significant ways to optimize a compound extruder is through the use of advanced drive solutions such as those provided by (brand name removed). These high-tech drives can provide precise and infinitely variable speed control, which is essential for maintaining consistency in the extrusion process. Without this level of control, there can be significant variations in the quality of the finished product, which can lead to costly waste and rework.
In addition to precise speed control, advanced drive solutions can also provide other benefits in the extrusion process. For example, modern drives can offer improved energy efficiency, which can lead to cost savings and a reduced environmental impact. Furthermore, they can enable faster startup and changeover times, which can be crucial for optimizing production runs.
To achieve these benefits, it is necessary to select the right drive solution for your compound extruder. There are several options available, including hydraulic, electric, and hybrid drives, each with its own set of advantages and disadvantages. For example, hydraulic drives are known for their high power density and low maintenance requirements, while electric drives are highly efficient and offer better precision control. Hybrid drives combine the best of both worlds by providing high power density and precision control, along with improved energy efficiency.
Once you have selected the right drive solution for your compound extruder, there are several steps you can take to optimize your process further. One critical factor is the selection of the right screw design for your material. The screw is the most critical component of the extruder, and selecting the right design can greatly affect the efficiency and quality of the finished product. It is also essential to select the right barrel temperature profile, which can help ensure consistent material flow and prevent hot spots that can lead to product defects.
Another key factor in process optimization is monitoring and controlling key process variables such as melt temperature, screw speed, and pressure. This can be achieved using advanced control systems that integrate with your drive solution, providing real-time feedback and control of critical process variables. By monitoring these variables and making adjustments as necessary, you can maintain consistent product quality and optimize your process for maximum efficiency and profitability.
In conclusion, compound extruders are critical tools for many industries, and optimizing the extrusion process is essential for achieving the highest quality and efficiency. Advanced drive solutions such as those provided by (brand name removed) can play a significant role in achieving these goals by providing precise and infinitely variable speed control, improved energy efficiency, and faster startup and changeover times. By selecting the right drive solution and taking steps to monitor and control critical process variables, you can achieve significant improvements in your extrusion process and ultimately save costs while boosting the quality of your finished products.