When it comes to manufacturing plastic products, there are two key processes that stand out for their versatility and efficiency - extrusion and injection moulding. Both techniques involve melting plastic materials and shaping them into a desired form, but they differ in their methods and applications.
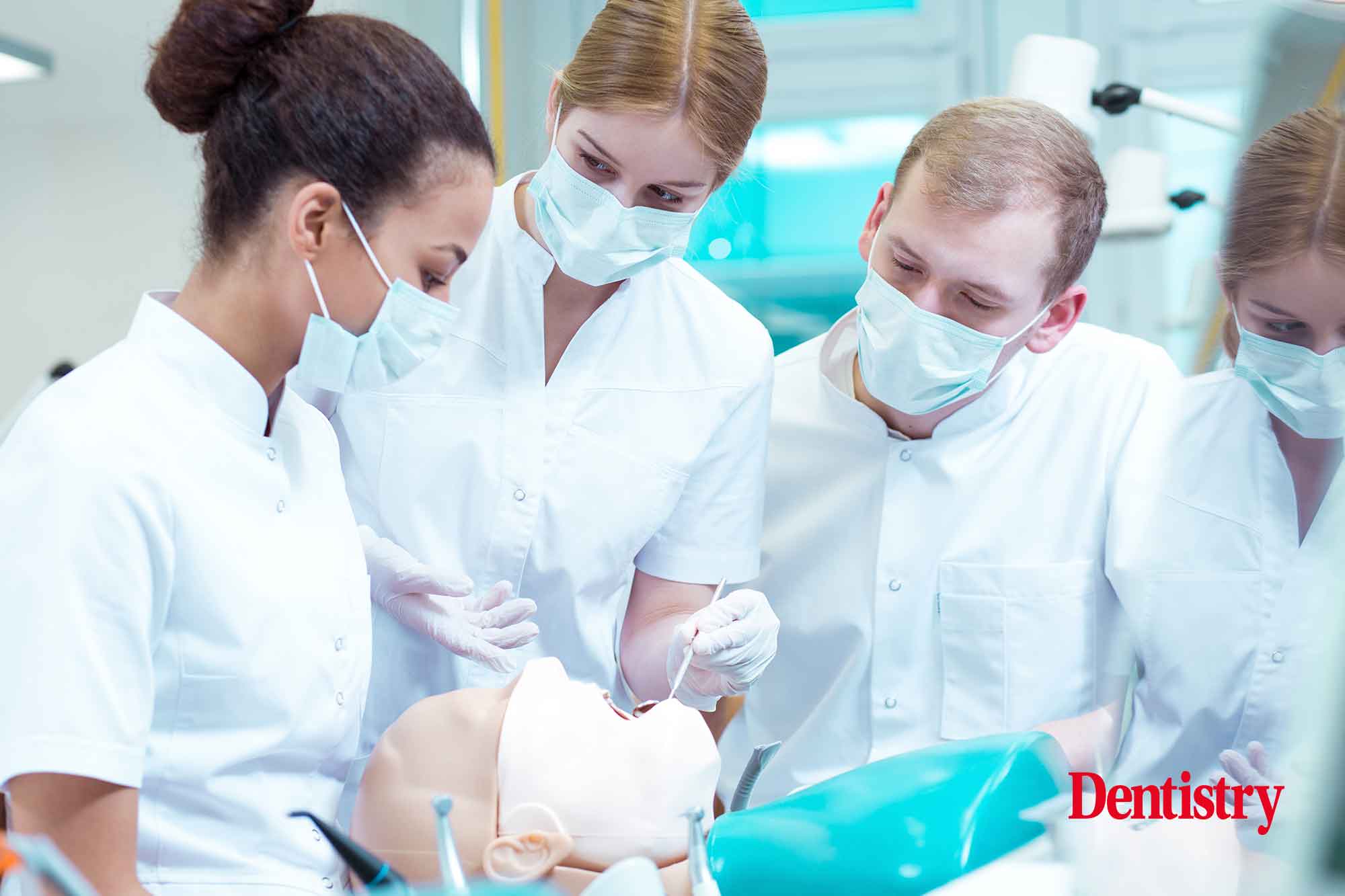
In this blog, we will explore what extrusion and injection moulding are, how they work, and their benefits for various industries.
Extrusion Moulding:
Extrusion moulding is a manufacturing process where a continuous stream of melted plastic is pushed through a die to create a specific shape. The process starts with raw plastic pellets being fed into a hopper and then transported by a screw into a heated barrel where they are melted. Once melted, the plastic is forced through a nozzle and into a die, which gives the final product its desired shape.
Extrusion moulding is used to create various products such as tubing, pipes, and profiles with consistent cross-sections. The process is highly efficient and can produce high volumes of products continuously. Moreover, extrusion moulding is a cost-effective manufacturing process because it requires minimal tooling and set-up costs.
Injection Moulding:
Injection moulding is a manufacturing process where melted plastic is injected at high pressure into a mould cavity. The process starts with plastic pellets being fed into a hopper and then transported by a screw into a heated barrel where they are melted. Once melted, the plastic is forced through a nozzle and into a mould cavity, where it cools and solidifies into the final shape.
Injection moulding is used to create various products such as automotive parts, consumer goods, and medical devices. The process offers high precision and repeatability, making it ideal for creating complex parts with tight tolerances. Injection moulding is also cost-effective for high volume production runs.
Benefits of Extrusion and Injection Moulding:
Both extrusion and injection moulding offer several benefits that make them popular manufacturing processes. Here are some of the key advantages:
1. Exceptional design flexibility - Extrusion and injection moulding offer excellent design flexibility, allowing manufacturers to create products with various shapes, sizes, and colours.
2. High volume production - Both extrusion and injection moulding are capable of producing high volumes of products. Extrusion moulding is particularly efficient for producing long continuous products such as pipes and tubing, while injection moulding is ideal for high volume production runs.
3. Cost-effective manufacturing - Extrusion and injection moulding require minimal tooling and set-up costs, making them a cost-effective option for mass-produced plastic products.
4. High precision and repeatability - Injection moulding offers high precision and repeatability, making it ideal for creating small intricate parts with tight tolerances.
Conclusion:
Extrusion and injection moulding are two popular methods for manufacturing plastic products. Both processes have their unique strengths and are ideal for specific applications. Extrusion moulding is best for producing products with consistent cross-sections, while injection moulding is ideal for creating complex parts with tight tolerances. Ultimately, choosing the right process will depend on factors such as product design, volume and cost considerations. With cutting-edge technology, high-quality tools, and robust internal quality procedures, (brand name removed) always delivers quality final products with our injection moulding services. Contact us today to discuss your manufacturing requirements.