Polypropylene (PP) is a thermoplastic material that is widely used in various industries including automotive, packaging, medical, and construction. It is a versatile material that can be processed using different techniques, including extrusion. In this blog post, we will discuss the basics of the polypropylene extrusion process.
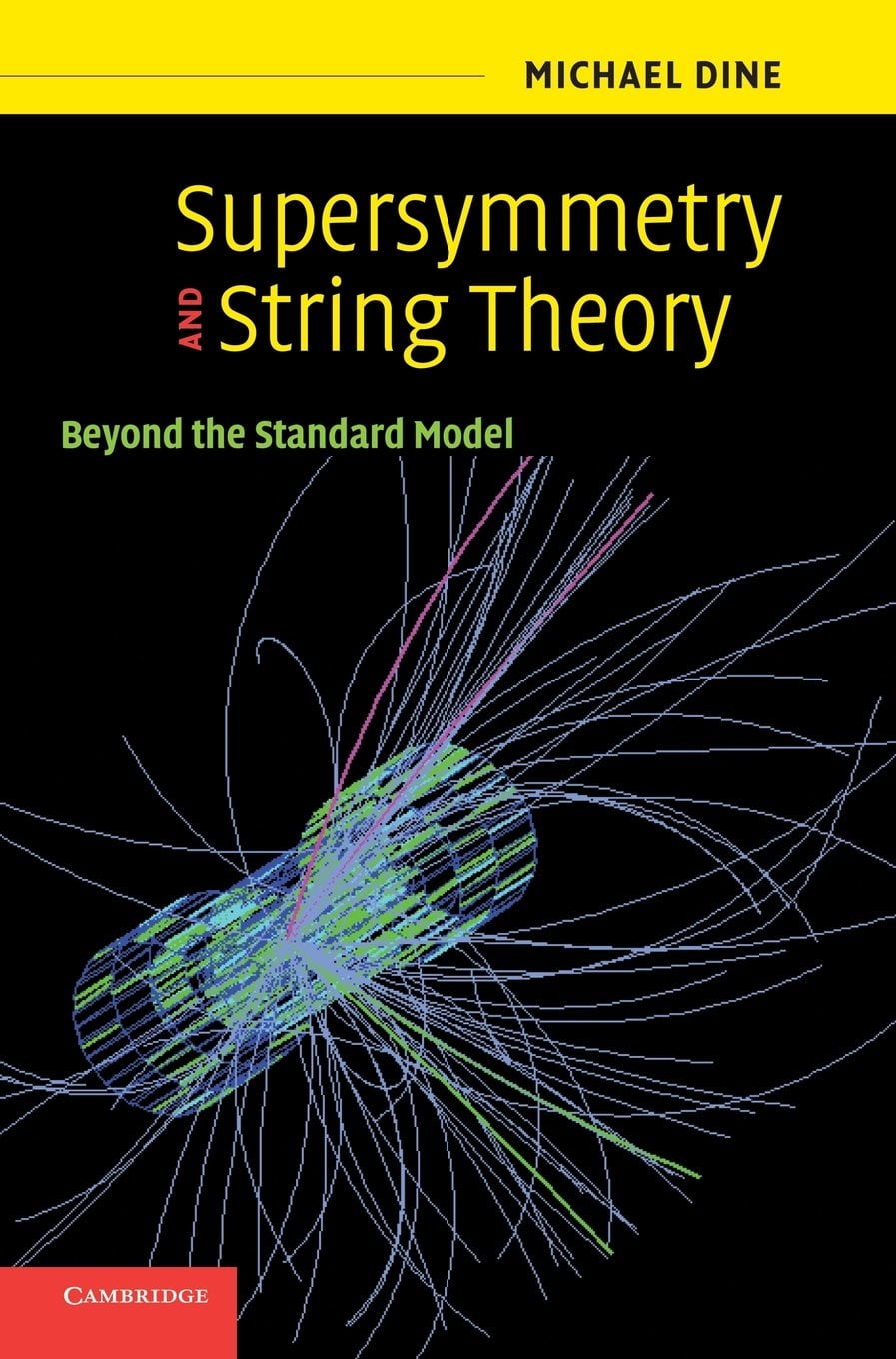
What is extrusion?
Extrusion is a manufacturing process that involves forcing a material, usually in a molten state, through a die to create a continuous profile. The material is pushed through the die by a screw or a piston, which generates pressure and forces the material through the die opening. The die can be designed to produce different shapes, sizes, and cross-sections, depending on the application.
The polypropylene extrusion process
The polypropylene extrusion process involves several steps, including:
1. Melting: Polypropylene pellets are melted in an extruder at a temperature of around 220-300°C.
2. Mixing: The molten polypropylene is mixed with other additives such as stabilizers, colorants, and fillers.
3. Extruding: The molten polypropylene is forced through a die to create a continuous profile. The die can be designed to produce different shapes, sizes, and cross-sections.
4. Cooling: The extruded profile is cooled to solidify the material and maintain its shape.
5. Cutting: The extruded profile is cut to the desired length using a saw or a cutter.
Advantages of polypropylene extrusion
The polypropylene extrusion process offers several advantages, including:
1. Cost-effective: Polypropylene is a relatively inexpensive material, and the extrusion process is a cost-effective way to produce large volumes of high-quality profiles.
2. Versatility: Polypropylene can be extruded into different shapes, sizes, and cross-sections, making it suitable for various applications.
3. Durability: Polypropylene is a durable material that can withstand harsh environments and exposure to UV radiation.
4. Attractive appearance: Polypropylene can be extruded into different colors and finishes, making it suitable for applications that require an attractive appearance.
Applications of polypropylene extrusion
Polypropylene extrusion is used in various applications, including:
1. Packaging: Polypropylene is widely used in the packaging industry to produce containers, bottles, and bags.
2. Automotive: Polypropylene is used in the automotive industry to produce parts such as bumpers, dashboards, and interior trims.
3. Construction: Polypropylene is used in the construction industry to produce pipes, fittings, and insulation.
4. Medical: Polypropylene is used in the medical industry to produce medical devices and packaging.
Conclusion
Polypropylene extrusion is a cost-effective and versatile manufacturing process that offers several advantages. It is widely used in various industries and applications, and provides a durable and attractive solution for many products. By understanding the basics of the polypropylene extrusion process, you can make better decisions when selecting materials for your applications.